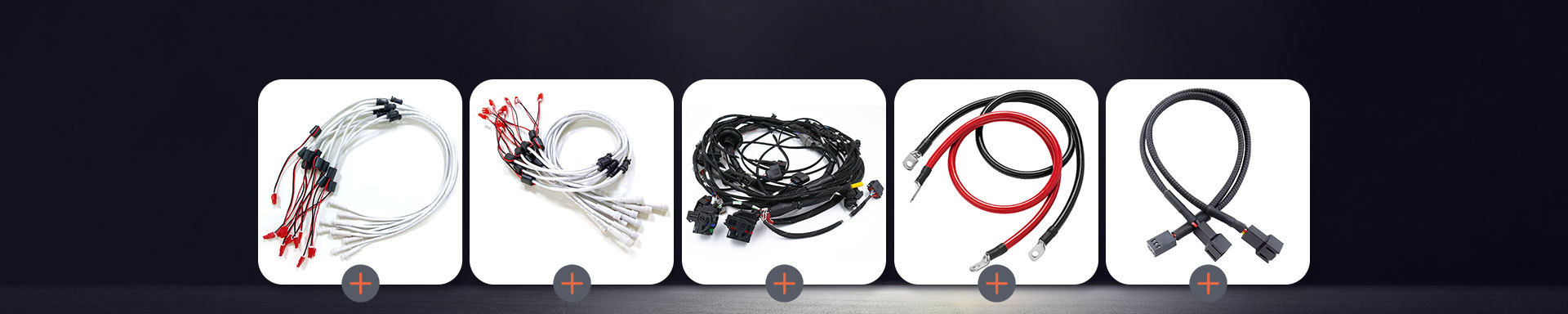
Essential Foundations of Electronic Wire Harnesses: A Comprehensive Overview
2024-08-12 16:15Wires and Cables: The core of a wire harness is made up of insulated conductors, which can be made from materials like copper or aluminum. These conductors are designed to carry electrical current or signals within an electrical circuit.
Connectors and Terminals: Connectors are the interface points of wire harnesses, facilitating connections between different components. They come in various types, such as plug and socket, pin and sleeve, and are tailored to fit specific applications.
Insulation and Jacketing: Insulation is critical for preventing electrical interference and short circuits. Materials used for insulation include PVC, TPE, and silicone, each offering different levels of protection and flexibility.
Protective Features: Additional protective elements like braided shielding, heat shrink tubing, and cable ties may be incorporated to enhance the durability and safety of the wire harness.
Design and Engineering: The first step in manufacturing is the design phase, where wire lengths, types, and routing are determined based on the application's requirements.
Cutting and Stripping: Conductors are precisely cut and stripped to the necessary length, with insulation removed at the points of connection.
Crimping: This process involves attaching terminals or connectors to the ends of the wires using a crimping tool, ensuring a secure and conductive joint.
Assembly: The individual wires are assembled into a harness, often involving the use of tools and equipment like wire strippers, crimping machines, and soldering stations.
Testing: Each harness is tested for continuity, resistance, and other electrical properties to ensure it meets the required specifications.
Automotive Industry: In vehicles, wire harnesses are used for engine management systems, lighting, infotainment systems, and safety features like airbags and ABS.
Aerospace: Aircraft and spacecraft rely on wire harnesses for critical control systems, navigation, and communication equipment.
Telecommunications: In this sector, wire harnesses are essential for networking equipment, base stations, and data transmission devices.
Consumer Electronics: From smartphones to home appliances, wire harnesses enable the connectivity and functionality of electronic devices.
Standards and Certifications: Adherence to industry standards such as IPC/WHMA-A-620 and UL standards is crucial for verifying the quality and safety of wire harnesses.
Quality Control Measures: Rigorous quality control processes, including visual inspections, electrical testing, and environmental testing, are implemented to ensure product reliability.
Risk Mitigation: Manufacturers must assess potential risks and implement strategies to mitigate them, such as using flame-retardant materials and designing for fault tolerance.
Continuous Improvement: Ongoing efforts to refine manufacturing techniques and materials contribute to the advancement of wire harness technology and safety.